high speed powder particles are cold-welded to a substrate
Cold gas spraying (developed from around 1950) is a process that generates relatively low temperatures compared to other additive processes. Powder particles are accelerated to around Mach3 speed via a gas stream and cold-welded to a substrate.
Cold gas spraying is characterized by:
- Localized, transient adiabatic shear instabilities at the interface
- Kinetic energy is converted into deformation and thermal energy.
- Rapid, highly localized, transient temperature increase at the interface -> drop in the yield point at the interface
- Short and highly localized plastic flow of particles leads to bonding.
- Localized microstructural changes initiate: work hardening vs. dynamic recrystallization
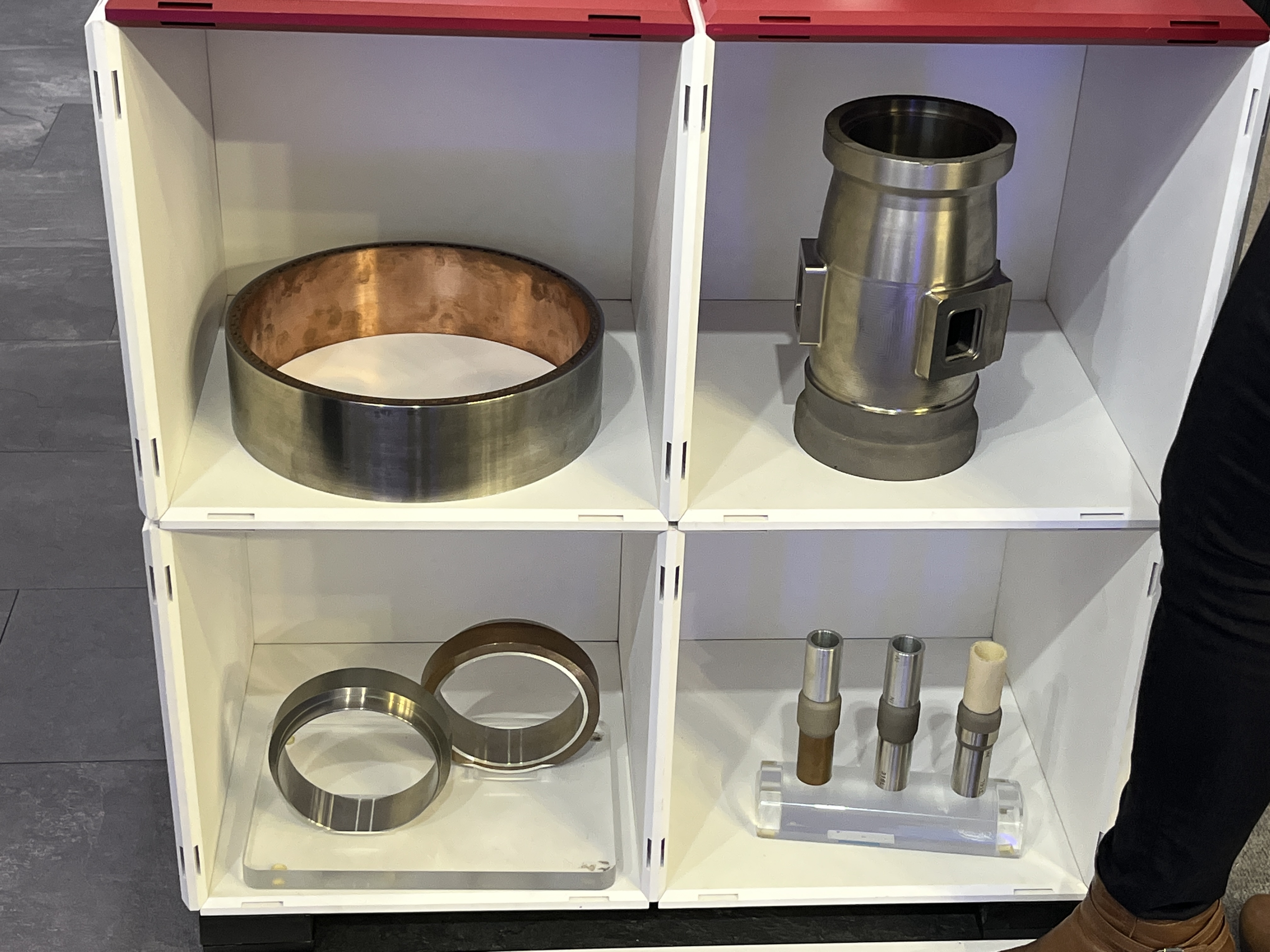
Typical materials
- Aluminum - Al, AA2024, A357, AA6061, AA7050
- Nickel - Ni, IN625, IN718, Invar36, NiCr, MCrAlY's
- Copper - Cu, CuCrZr, CuAg, CuAl, CuSn, CuZn
- Steel - 316L, 430L, M3/2, M152
- Titanium - Ti, Ti64, TiAl
- Precious metals - Ag, Au, Pt
- Refractory metals - Nb, Ta, Zr, Mo, Cr
- Others - Zn, Sn, Cermets
- Ceramics
and many more!