Glasses are solid materials that have no crystal structure. This means that the atoms do not form a lattice, but are arranged randomly at first sight: they don't have a long-range order, but at best a close-range order. This is called 'amorphous structure'.
Like all glasses, amorphous metals are created by preventing natural crystallization. This can be done e.g. by rapid cooling of the melted metal, so that the atoms are stripped of their mobility before they can form a crystal arrangement. However, in metals, this is particularly difficult since it requires unrealistically high cooling rates in most cases due to the special chemical bonding mechanisms. With metals that consist of only one element, it is, to date, impossible to produce a metallic glass because even at a low temperature the mobility of the atoms is still so high that they will inevitably crystallize. The only known amorphizable metals are alloys of at least two elements (e.g., AuIn2). Even today, only special alloys (usually close to the eutectic point) of several elements, for which the necessary cooling rate is achievable, hold technical relevance as amorphous metals. The cooling rate for the first metallic glasses was still up to 106 K/s.
Metallic glasses show the typical metallic light reflection and cannot be distinguished from ordinary metals by the untrained eye. Their surface is especially smooth and does not scratch easily due to the high hardness, therefore a particularly beautiful and lasting shine can be achieved.
Metallic glasses are harder than their crystalline counterparts and have high strength. Small deformations (~1 %) are purely elastic. This means that the absorbed energy is not lost as deformation energy, but is fully released when the material is springing back (hence the use e.g. in golf clubs). However, the lack of ductility also makes them brittle: if the material fails, it happens suddenly and by breaking, not by bending like a metal.
The corrosion resistance is usually higher than for metals of comparable chemical composition. The reason for this is that corrosion usually attacks grain boundaries between single crystallites of a metal, which amorphous materials lack.
There are non-magnetic and magnetic amorphous metals, some of which are the best commercially available soft magnetic materials.
Medicine: Scalpels (especially ophthalmic ones) made of amorphous metal are already available. They can be sharpened more than those made of stainless steel because of their great hardness, and they retain their sharpness even longer. Due to the material's biocompatibility, high strength at a relatively low weight, and resistance to wear, surgical implants are being considered.
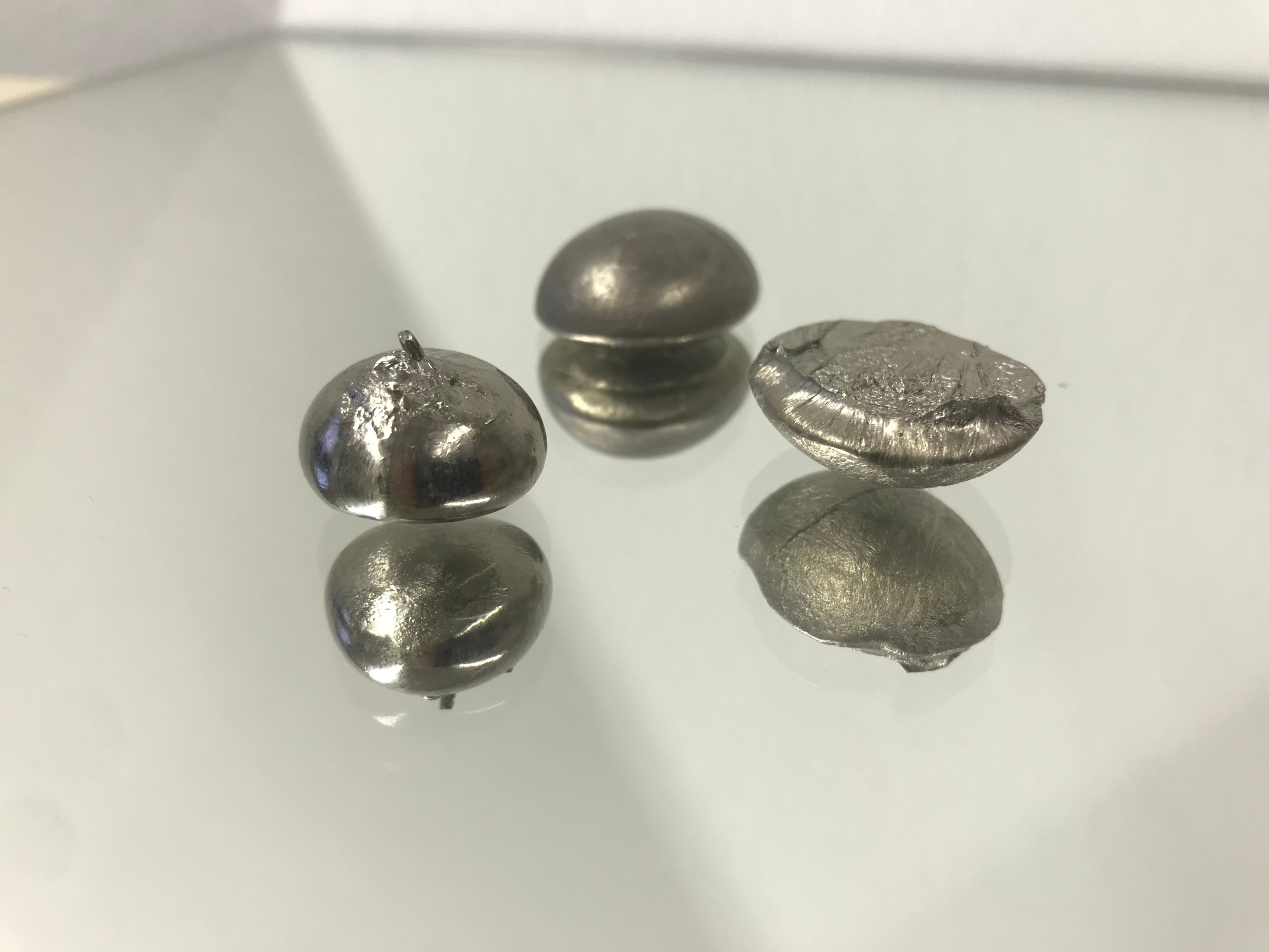
Consumer electronics: The smooth, shimmering, scratch-resistant surface of metallic glasses led to their use in the cases of exclusive mobile phones, MP3 players, and USB sticks. Their high strength (better than titanium) allows for thinner walls, thus lower weight and even more miniaturization. Injection molding leads to more freedom in design and cheaper processing, compared to stainless steel or titanium which need to be forged. Dainty mobile phone hinges, where large forces act on the smallest components, benefit from the superior mechanical properties of metallic glasses.
Material finishing for industrial applications: The surfaces of conventional materials can be made harder, more resistant, and less prone to wearing by coating them with amorphous metals (commercial example: Liquidmetal Armacor Coating).
Jewelry: Some metallic glasses are made of precious metals (such as platinum), but are much harder and therefore do not scratch easily. The special processing options allow for shapes that are difficult to achieve with conventional metals.
Sports equipment and leisure items: Golf clubs were one of the first commercial products from amorphous metal in 1998. The company Liquidmetal used them to introduce the material to the market through large-scale advertising campaigns (featuring the PGA TOUR professional golfer Paul Azinger). Golf clubs benefit mainly from the unrivaled elasticity of amorphous metals. In development (although only partially commercialized yet) are tennis and baseball bats, fishing equipment, skis, snowboards, bicycles, and sports rifles.
Aerospace: Due to generally high costs and safety as the highest priority, material cost has little significance in these areas. Metallic glass is considered wherever its outstanding characteristics could play a beneficial role. Some parts of the solar wind collectors on the Genesis probe were made of amorphous metal.
Military: Numerous developmental projects, especially ones conducted by the US Department of Defense, are testing the use of amorphous metals for various applications. Tungsten-based metallic glasses, due to their high hardness and self-sharpening behavior, are expected to replace conventional tungsten alloys and depleted uranium in armor-piercing kinetic energy penetrators. In military aviation, amorphous metal coatings are said to increase the hardness and corrosion resistance of lighter metals such as aluminum and titanium.